
Condition Monitoring Services
Vibration Analysis
Vibration analysis is defined as a process for measuring the vibration levels and frequencies of machinery and then using that information to analyze how healthy the machines and their components.
We monitor all rotating equipment’s with latest dual channel analyzers to pinpoint exactly the source the vibration in all major segment of industries.
Typical problems which can be identified includes :
- Unbalance
- Bearing failures
- Mechanical looseness
- Misalignment
- Resonance and natural frequencies
- Electrical motor faults
- Bent shafts
- Gearbox failures
- Empty space or bubbles (cavitation) in pumps
- Critical speeds

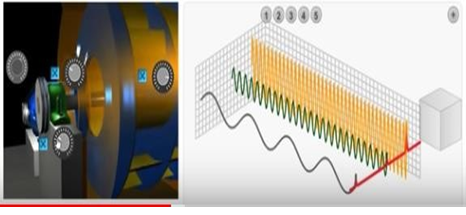
Service offered include AMC contracts , On call basis , In house expert deployment and IOT based Remote Monitoring .
Executive Summary will be shared with top management to have an overview about Equipment health condition and Maintenance team will be provided with detailed report clearly indicating the source of vibration and necessary corrective action which needs to be planned with priority.
Thermography
- Infrared thermography is the science of acquisition and analysis of thermal information by using non-contact thermal imaging devices.
- The use of electronic “cameras” to detect radiant energy or heat.
- Produces a visual image called a thermogram (or heat picture).
Thermography is the science of seeing heat patterns using special electronic cameras. Rather than seeing light, these remarkable instruments create pictures of heat. They measure infrared (IR) energy and convert the data to images corresponding to the temperature.
Safety :
Opening panels and doors for infrared inspection of live electrical installations greatly increases the risk of arc-flash injury. Ensure proper PPE as per arc flash rating.
Typical Electrical Applications :
- (3 phase) Power distribution
- Fuse boxes
- Cables & connections
- Relays/Switches
- Insulators
- Capacitors
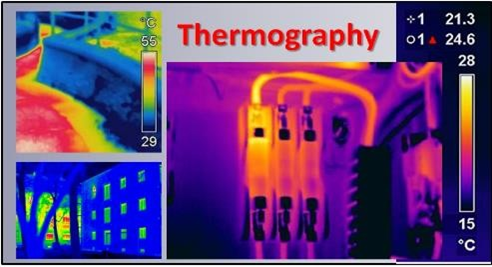
- Substation
- Circuit Breakers
- Controllers
- Transformers
- Motors
- Battery Banks
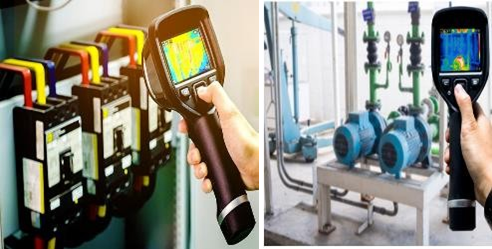
Lubrication Management & Oil Analysis
The lubrication management concept takes a holistic approach to lubrication. In this approach, lubricants are considered not as consumables to be purchased at the lowest price, but as an asset to be managed and nurtured. This nurturing process starts the day the lubricant arrives onsite and ends the day the oil is drained from the component and disposed of appropriately. In doing so, the key areas to consider include:
- Lube standards, consolidation and procurement
- Lube storage and handling
- Oil sampling techniques, Contamination Control & Lubricant analysis
- Training, skill development and certification
- Lubrication/ re-lubrication standards and best practices
- Program management
- Procedures and guidelines
- Program goals and metrics
- Safety and disposal guidelines and best practices.
- Continuous improvement.
Assessment will be performed in your facility to understand your existing practices and compare your standards against industrial benchmark to identify the gaps and work on area of improvement.
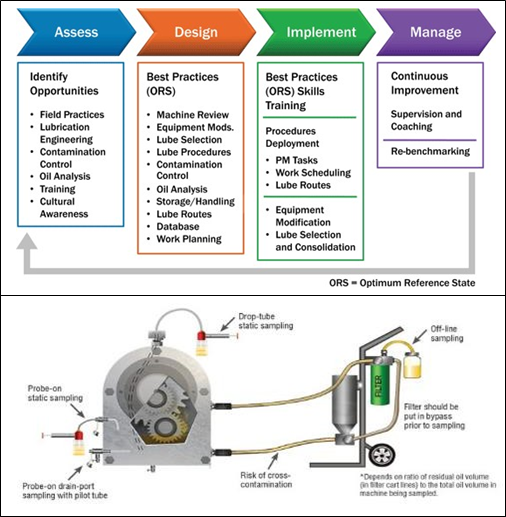
Oil Condition Monitoring
The main cause of equipment failure is due to
- Incorrect Lubrication,
- Foreign material,
- Corrosion,
- Bearing failure,
- Inadequate maintenance,
- Continuous / shock overloading.
Lubricants apart from performing its vital functions, it helps to measure performance ability and gives indication of machine health condition. Some of the key parameters tested are:
- Viscosity
- Viscosity Index.
- Total Acid No.
- Total Base No.
- Water Content
- Wear Debris Analysis
Your Critical Equipment oil sample will be tested in NABL Accredited lab facility as per standard protocols and clear recommendations will be proposed pinpointing the root cause.
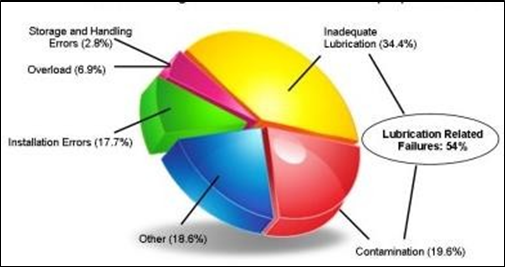
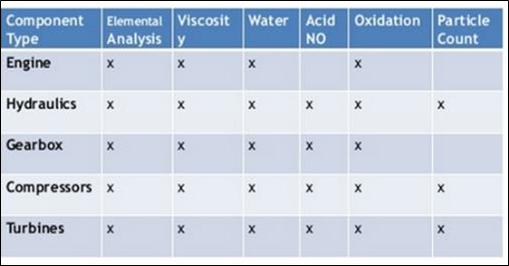